Cost vs. Benefit: Is a Software Tool for ISCC Mass Balance Worth the Investment?
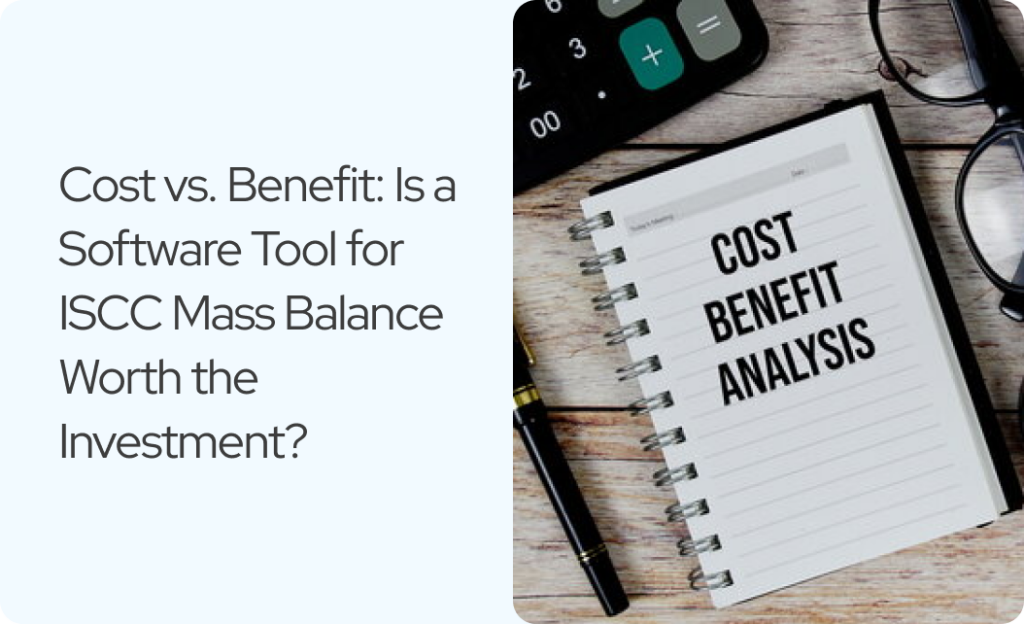
With ISCC certification becoming the norm for sustainable supply chains, companies, especially in chemicals, plastics, and materials—face a clear choice: keep struggling with spreadsheets or invest in a smarter system.
ISCC Mass Balance Bookkeeping isn’t just a compliance task anymore. It’s central to credibility, growth, and access to premium markets. But how do you know if a software solution is actually worth it?
Let’s break it down.
The Real Cost of Manual ISCC Bookkeeping
Manual tracking might look cheap, but it’s far from it. Here’s what you’re really paying for:
1. Admin Time That Adds Up Fast
On average, a single ISCC-certified site spends 20–40 hours a month on data entry, credit tracking, and reporting. As ISCC-certified operations grow, so does the burden of manual tracking, often requiring 1.5–2 FTEs per year. That’s $120K–$240K spent on just maintaining spreadsheets.
2. Audit Risk and Errors
Manual allocation errors and miscalculations are common and costly.
A failed ISCC audit or incorrect declaration can cost anywhere from $10,000–$50,000 in remediation, rework, and lost business.
3. Slower, More Expensive Scaling
As your product lines grow, manual systems hit their limits.
Hiring extra staff just to maintain compliance isn’t sustainable. Every expansion compounds complexity and cost.
4. Talent Drain
Skilled sustainability or compliance professionals spend time updating cells instead of improving operations. That’s thousands of hours lost to low-value work.
How Software Pays for Itself: ROI Scenarios
Let’s run some example numbers to compare the ongoing cost of manual operations vs. software-enabled automation.
Scenario A: Small to Mid-Sized Chemical Manufacturer (1–3 Sites)
Metric | Manual Tracking | With Software |
Admin Cost | $80,000–$150,000/year | $15,000–$30,000/year |
Audit Prep Time | 6–8 weeks | <1 week |
Staff Needed | 1–2 FTE | 0.25–0.5 FTE |
Annual Savings | $40,000–$80,000 | |
Payback Period | < 12 months | |
2-Year ROI | 200–400% |
Scenario B: Enterprise-Level Manufacturer (4+ Sites)
Metric | Manual Tracking | With Software |
Admin Cost | $200,000–$400,000/year | $40,000–$75,000/year |
Audit Prep Time | 3–4 FTE | <1 week |
Staff Needed | Months | 0.5–1 FTE |
Annual Savings | $125,000–$265,000 | |
Payback Period | ~6–9 months | |
2-Year ROI | 300–600% |
Beyond the Numbers: Strategic Upside
Software isn’t just about doing the same thing faster—it changes the game entirely.
- Real-Time Visibility: Live dashboards help you track allocation, material flows, and certificate validity across all sites.
- Audit Confidence: Documentation and declarations are always ready, reducing audit stress by up to 90%.
- Scalability Without Headcount: You can grow your ISCC-certified operations without hiring more people to keep up.
- Regulatory Resilience: As ISCC updates requirements, your system updates too—without needing to retrain your entire team or reinvent your workflows.
- Faster Decisions: Real-time data empowers operations, procurement, and sustainability leaders to move faster and with confidence.
Final Thoughts
ISCC Mass Balance compliance may not be glamorous, but it’s foundational. And automating it unlocks serious savings, smoother audits, and future-ready infrastructure.
In short, manual bookkeeping costs more than you think, and delivers far less than you need.
With the right software, you’re not just getting a tool. You’re getting time back, reducing risk, and setting your team up to scale, faster and smarter.